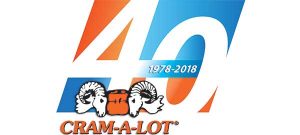
J. V. Manufacturing implemented lean practices approximately seven years ago. At that time several member of management traveled off site to receive training then returned to implement practices. Evidence of their efforts are obvious. Variations of cellular production, workplace organization, 5-S, just in time materials, and one piece flow are seen throughout the operations. In order to remain competitive it is now time to advance the training, reset the bar, and identify the next opportunities. They have submitted a request to the Arkansas Economic Development Commission Manufacturing Solutions (AEDCMS) asking for assistance in addressing Lean Manufacturing training needs and support to facilitate a Lean Transformation.
Because J.V. Manufacturing had already been successful in creating and implementing lean practices, the focus this time was to educate team members in the principles and application of lean manufacturing. Manufacturing Solutions’ approach included training on specific subjects to help the team learn specific lean tools, facilitation of Kaizen Events to create a line that meets customer demands, and coaching to help sustain the gains already achieved and allow the team to move more confidently into the future. Employees underwent Lean Manufacturing 101 training, value stream mapping training, and KATA training and implementation.
Company: JV Manufacturing
J.V. Manufacturing, Inc., of Springdale, AR manufactures CRAM-A-LOT® Solid Waste & Recycling Equipment for commercial applications and employs approximately 220 employees. The family-owned business has a history of caring for its employees, and the company’s policies are family-focused. Employees with school-aged children, for example, are allowed time off with pay to participate in school activities. The company is passionate about providing safe, quality products and outstanding customer service.
We contacted AEDCMS with the intent to train new employees and refresh some of our older employees on the fundamentals of Lean Mfg. As a result we have reduced our overtime hours to 9% with the goal of 5% or less still in reach. We are very excited here at Cram-A-Lot® about seeing this project come together and achieving our company goals while expanding the use of Kata and other Lean principles throughout our organization.
